Spiralbanding FAQ (Frequently Asked Questions)
SpiralbandingTM FAQ (Frequently Asked Questions)
- Why should we consider applying Spiralbanding to our drill pipe?
The value in protecting and increasing the life of the tube of drill pipe by 2 to 3 times with a single application of Spiralbanding provides cost savings that can save millions of dollars a year per rig. This application is focused primarily on the lateral section which eliminates rotation of drill pipe from the vertical to the lateral sections of the well and keeps all of the pipe in premium condition. There could be additional benefits depending on drilling conditions and practices including: less fatigue of the pipe due to reduced buckling, increased weight on bit, reduced torque and drag, and additional circulation of fluids and cuttings.
- What testing has been conducted on Spiralbanding?
Aside from hundreds of thousands of feet of downhole testing that has been performed since 2019, extensive metallurgical and structural laboratory testing has been conducted to ensure that the performance of the drill pipe has not been compromised due to the Spiralbanding application.
- Does Spiralbanding eliminate the ability to inspect the drill pipe tube?
In the area of the Spiralbanding, magnetic particle inspection procedures are used, which are similar to the procedure used on Heavy Weight Drill Pipe and Wear Knot™ Drill Pipe center wear pads.
- Why is the wear protection applied in a spiral configuration?
The patent pending spiral orientation removes the isolated transverse stress created by concentric bands. Testing has proven that applications of circular bands create stress concentration locations at the transition from the hardband to the tube body. Much like the internal upset area on tool joints or transverse slip cuts, these become the highest failure point on drill pipe tubes. This also creates another restriction for circulation and provides no stability for flex. More flex equals more fatigue on stress areas.
- Are there any additional benefits of Spiralbanding besides just reducing wear of the pipe body?
Yes, we are currently observing benefits in the amount of weight that can be transferred to the drill bit (weight on bit) due to the reduction in buckling and deflection in the drill string. Also, there is evidence of reduced drag because the body of the drill pipe doesn’t interact with the formation as frequently. Some have commented that the spiral design of Spiralbanding will assist in circulating fluids in the well bore.
- Why hasn’t anyone else welded on drill pipe before Spiralbanding?
With the recent advancements in welding equipment, the opportunity to weld on the body of drill pipe without compromising the base steel has recently become possible. Previous welding technologies could have been harmful to the structural integrity of the drill pipe.
- Is reapplication of Spiralbanding a possibility?
It is possible to reapply Spiralbanding numerous times. It must be understood however that another aspect of the drill pipe may be compromised due to fatigue or wear in the drill pipe, tool joint, friction weld, etc.
- Is there eccentric wear on the Spiralbanding similar to what we see on drill pipe?
Eccentric wear is a common occurrence on drill strings. The Spiralbanding will eccentrically wear much the same as the drill pipe body and tool joints. Eccentric wear will always exist, however by increasing rigidity and stability of the drill string, this will help control buckling and reduce uneven wear.
- Does Spiralbanding affect the metal of the drill pipe?
The revolutionary welding technology used in Spiralbanding reduces the heat input and depth of the heat affected zone (HAZ) such that the integrity of the tube is not compromised. The combination of the new welding technology along with the spiral design reduce any adverse effect that could impact the structural integrity of the drill pipe tube.
- Will Spiralbanding affect the internal plastic coating (IPC) of the drill pipe?
There is currently progress on refining a procedure and upgrading equipment to protect the IPC. At this point, all of our customers have been more concerned with prolonging the life of their drill pipe than internal pipe corrosion due to the lack of an IPC.
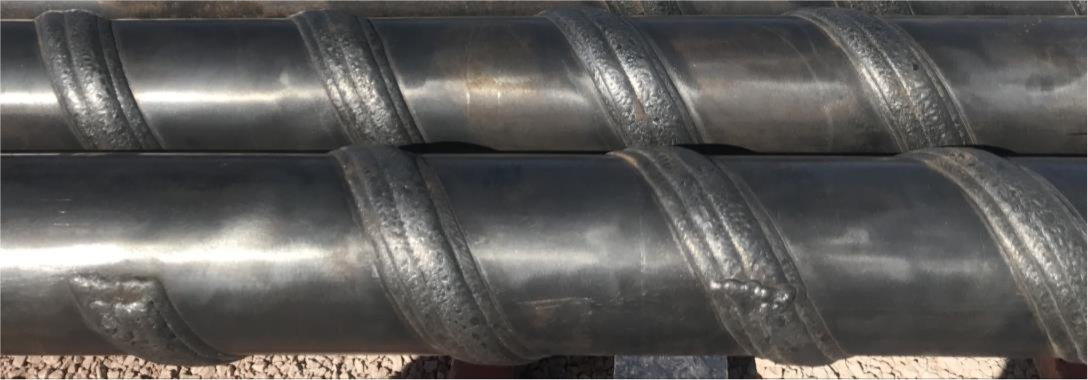